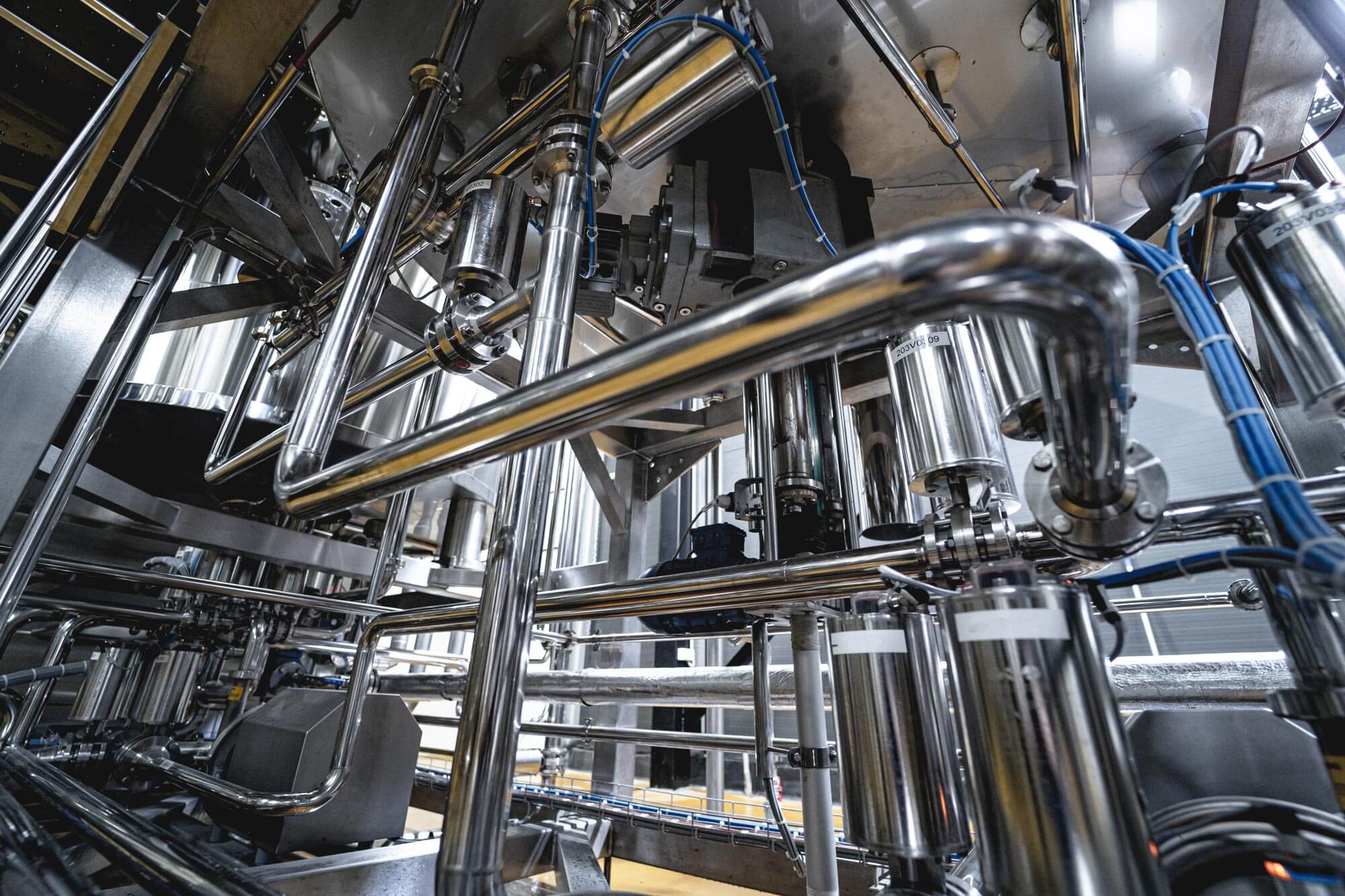
Welcome to Paratherm
Premier Heat Transfer Fluid Technology
Engineered Fluids
Proven, advanced formulations ideal for your processes, industry, and applications. More choices and better choices in heat transfer fluids based on our 30 years in this business.
Find Out More24/7 Response
Quick, knowledgeable answers on fluid selection. Rapid turnaround on lab tests. Products stocked strategically for faster delivery. 24/7 contact center for emergencies. Just the beginning of Paratherm superior responsiveness.
Learn MoreExpert Support
Technical and engineering experts with decades of real-world indirect heating experience. We know what goes wrong, how to fix it, and how to stop it from happening again. We know heat transfer for your industry (cold) and hot.
Contact UsHeat Transfer Fluid Technology Backed By Superior Service
Not all heat transfer fluids, or the companies that provide and service them, are created equal. Paratherm offers only the best fluid formulations, then backs them up with proactive services and industry-leading expertise. With hundreds of years of cumulative heat transfer experience, we’ve perfected the art of customer service and the science of heat transfer technology. That’s what our customers say. We invite you to experience our fluid technology and solid service.
We deliver exactly what you need for ongoing reliable performance
From fluid analysis to initial and ongoing training, troubleshooting to technical expertise and documentation, as a thermal heat transfer fluid manufacturer, Paratherm provides more added-value, no-cost services to our customers.
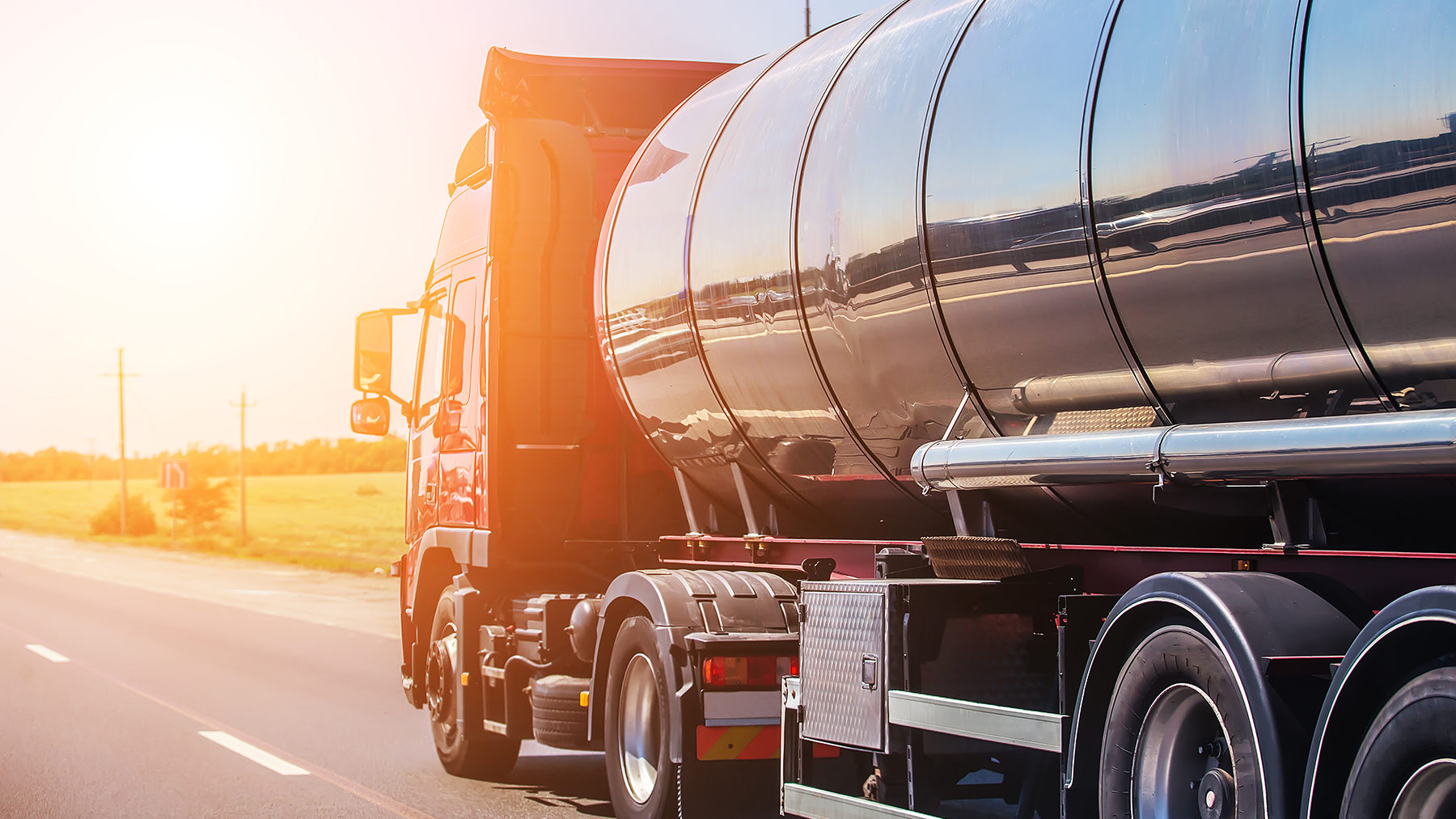
Paratherm Delivers. See how Paratherm is different and better.
Have a big system? Paratherm supplies the best products and services, delivered with expertise. Bulk Shipments are available and customed to fit your schedule.
Industries Served
Paratherm offers more for more industries – for heating, cooling, and temperature transfer
News
-
Bolstering Fire Safety
Edward Cass, Paratherm, USA, explains how the risk of fire in thermal fluid systems can be minimised.
-
Learn how Routine Fluid Analysis Can Extend the life of your system
Routine Testing and fluid analysis is vital to ensure your equipment is in the best possible shape.
-
3 Key Strategies for Maximizing Performance of Heat Transfer Fluids
Ed Cass, MLT I, Paratherm’s Technology Manager, discusses key strategies for increasing your heat transfer fluid performance.